Online Technical Training Blog
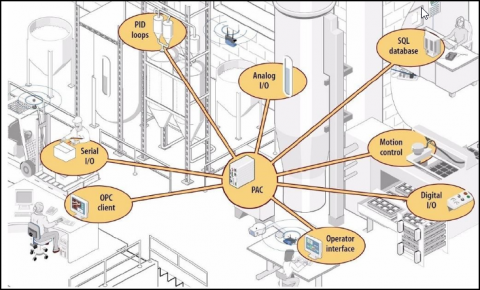
PLC vs. PAC: Understanding the Differences & Values of Each
In some ways, the phrase, “if it ain’t broke, don’t fix it” is an adage that can be applied to the manufacturing sector, particularly when it comes to the use of Programmable Logic Controllers (or PLCs). Since the 1960’s, PLCs have been used to automate manufacturing processes – and while the PLCs of today dwarf the capabilities from those in operation sixty years ago, many believe that as far as process management is concerned, there is no better solution than a Programmable Logic Controller.
Though many argue that a PAC, or Programmable Automation Controller, is just a PLC with a new, modern name (a term originally coined in 2001 by the ARC Advisory Group), there are those who believe that PACs offer greater value than the tried and true PLC, and vice versa. Ultimately, deciding who is right and who is wrong comes down to identifying what is the right system for the end user’s desired application.
What's the Difference Between a PLC and PAC?
A PAC can be described as a ‘hybrid’ of a PC and a PLC in that it typically offers the benefits of both in a single package. One major difference between a PLC and PAC is the programming interface. Most PLCs are programmed in a graphical representation of coils and contacts called Ladder Logic. PACs can be programmed using ladder logic, but also have the capability to be programmed in computer programming languages such as C or C++.
Where PLCs are generally accepted to excel is in simple or high-speed machine control applications. A common PLC device operates with limited memory and focuses on discrete inputs/outputs with on/off control.
PACs, for their part, are more often than not deemed more suitable than PLCs in complex automation system architectures that commonly contain several advanced PC-based applications including but not limited to asset management, more advanced process control, and human machine interface functionality. PACs are also characterised as being much more flexible from a programming perspective, and are known to contain more features in general.
PACs also make expanding the system much easier than a conventional PLC unit, simplifying the process by which users must add and remove sensors – oftentimes without requiring the user to disconnect any wiring.
Clearly, there are some definite and tangible differences between the applications of a Programmable Logic Controller and a Programmable Automation Controller that go well beyond the use of a shiny new moniker. That being said, it is important to return to a sentiment that was expressed above: the best system is the one that is right for the job.
With that thought in mind, PLCs are arguably best suited for simple tasks like controlling a basic industrial machine. To be clear, this is not to disparage the functionality of PLCs in any way, shape, or form – rather, it’s a statement suggesting that users not buy more functionality than is needed. Most of the world’s automated manufacturing is done through the use of PLCs because they simply don’t need all the functionality and applications afforded by a PAC in order to complete the manufacturing process.
Now, if the desired application requires controlling a substantial number of input and output points, or if the application is one that is much larger in scale and requires extensive loop control, a PAC just might be the way to go.
To recap PACs and PLCs share several commonalities including power supplies, CPUs, I/O racks and I/O modules. Both machines have memory and addressing that reflect individual I/O points on the modules. However, the differences are very significant:
- Many PLCs have fixed memory maps and addressing. While some PLCs, such as Rockwell’s Logix 5000 and Siemens S7 use tags, many PLCs do not. All PACs use tag names and have memory map constraints.
- PACs typically have much greater I/O capacity and memory size than PLCs.
- PACs offer communication and data handing options, such as USB data logging ports, web servers, and data log files.
- PACs are designed to be integrated more tightly with SQL and other databases. They offer 16-bit analog resolution for all analog processing requirements.
The nice thing about either system, whether PLC or PAC, is that once the user has settled on the type of system, there are a large number of models to choose from, ensuring that the right one can be found. This is because PLCs and PACs are designed to account for an application’s scale, typically based on input and output counts.
As time progresses, many key differentiators between PLCs and PACs are becoming less pronounced because PLC technology continues to evolve, arguably providing today’s workforce of PLC programmers an abundance of challenging and interesting opportunities. To say that PLC technology will very soon give way to the power of microprocessors is a bit of a reach, considering that many manufacturers around the world still use manual methods in their processes, making it highly unlikely that when it comes time to upgrade their operations, they’ll leapfrog right past PLC integration and go straight for a more substantive, albeit much more costly PC-based alternative.
One could even argue that the industry will see a resurgence in PLC use as manual manufacturing methods become more and more antiquated. Of course, this will bring with it a demand for additional PLC technicians to service and maintain these valuable systems.
By enrolling in George Brown College’s PLC Technician Certificate program, students will learn the fundamental skills necessary to be able to work with a wide number of Programmable Logic Control systems already in use in thousands of industrial environments worldwide.